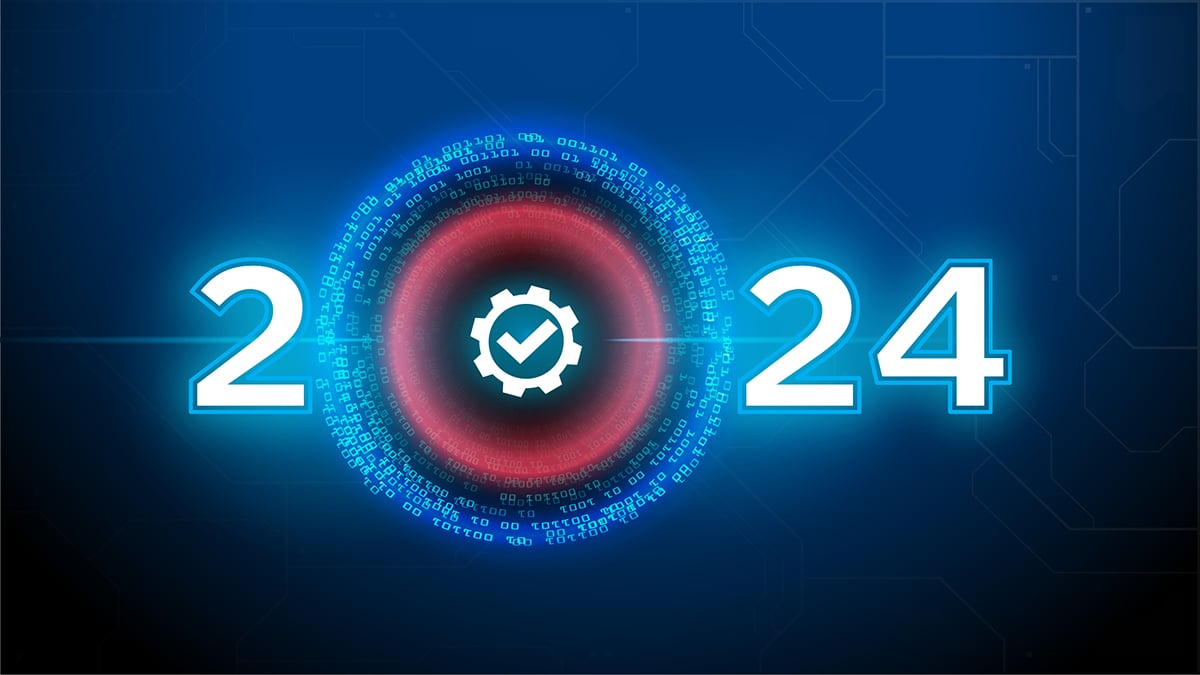
Introduction
Manufacturing operations face many challenges that span from keeping pace with digital technologies to updating or migrating legacy systems, managing the supply chain, meeting customer expectations, incorporating safety, cybersecurity and sustainability measures, and more. Combined with labor shortages, these issues can disrupt daily operational routines and high-priority projects, such as non-routine startup and commissioning efforts and shutdowns, turnarounds or outages (STOs).
To keep operations up and running, manufacturers are having to extend the lifecycle of their existing equipment. Maintenance activities alone carry their own set of safety risks, especially when limited resources is an issue.
By taking a holistic approach, manufacturers can mitigate risks and ensure operational, maintenance and future startup, commissioning and STO goals are met. They need an upfront plan that follows maintenance best practices and involves the right crew mix.
Plan and Prepare Early – No Shortcuts!
Manufacturers often have rigid project deadlines and need to get tasks done sooner rather than later. However, a “get it done fast” or “finish it now” mentality pressures people to reactive decision-making, prompting shortcuts that sadly bypass important quality assurance (QA) and quality control (QC) checks. Without a proper plan in place, companies often find themselves making last-minute decisions and changes, which can lead to project schedule delays, increased costs, and the potential for safety risks to become a reality.
No matter the size of the project, a comprehensive upfront plan and well-defined scope is required. Proper planning helps align the team and performance expectations, while keeping short- and long-term strategic goals in mind. Projects can be managed skillfully with the right team, so they get completed on time and on budget.
During the planning process, all risks should be identified and tracked with mitigation and contingency plans in place. This is a fundamental aspect of managing risks and tends to get minimal attention. Some contributing factors include lack of personnel experience, missing components for the job and not engaging enough people or key stakeholders early on.
A much leaner workforce often means the same people must perform and execute multiple tasks in parallel. Engineering teams typically lead capital expenditure (CapEx) project efforts to get all started on time and implemented. Maintenance and operations teams usually have their own large list of tasks that must be completed at the same time. A maintenance plan should outline the work to be done, such as repairing, refurbishing and reutilizing assets and performing instrument calibration, substation maintenance and internal equipment cleaning.
To ensure a successful maintenance plan and preparation process, be sure to follow these best practices:
- Identify problems and define scope deliverables in as much detail
as possible with early engagement - Determine priority tasks and gather and document required
specification information, such as:- Piping and instrumentation diagrams (P&IDs)
- Instrument specifications
- Single line diagrams
- Loop sheets
- Other pertinent design documents
- Identify existing instrumentation that can be refurbished or
reutilized in all areas due to supply chain issues - Establish rigid QA and QC practices – don’t compromise on them!
- Ensure identification of potential problems and long lead time items
- Identify critical safety instrumented systems (SIS)
- Avoid duplicated effort
- Develop progress tracking tools
- Perform location walk-down to visually identify all new and
existing instruments, valves, motors, and other electrical control
devices prior to active testing - Conduct daily status meetings during outages or critical junctures
- Provide appropriate supervision to drive accountability
Implementing a solid plan and following best practices helps identify critical instrumentation that can be refurbished, repaired, reutilized and recalibrated for different applications or areas of the plant. This approach can help keep maintenance schedules and outages flowing with more efficiency. When lack of resource bandwidth and supply chain issues delay high-priority maintenance activities, the process can be stressful for existing personnel who are already overwhelmed. In these instances, third-party expertise may be required.
The Right Team Makes a Difference
Many companies underestimate the positive impact the right crew mix can have in guiding a project to completion. Oftentimes even the best laid plans and technical assumptions can lead a team in the wrong direction, resulting in system outages, lost productivity and significant costs. When putting a team together, look to include a variety of people from different functional areas who have experience in maintenance, calibration, startup and commissioning and STO projects.
For those facilities lacking the resource bandwidth or expertise to perform these types of services, consider engaging an experienced third-party partner early in the planning stage to work alongside the maintenance team to ensure a successful project that stays on time and on budget. Someone who has the required expertise and technical depth to help navigate through the decision-making process and deliver a maintenance solution that aligns with company expectations and specific requirements.
The right partner can take a holistic approach to the project and help identify and evaluate critical items that can cause schedule delays, as well as work through any operational and business challenges from start to finish, preventing unnecessary and costly changes later.
- Offers process control equipment calibration consulting and instrument calibration services
- Provides National Institute of Standards and Technology (NIST) traceable calibration
- Identifies existing instrumentation, devices and equipment that can be refurbished and utilized to eliminate scope gaps caused by supply chain issues
- Calibrates instruments to eliminate errors in readings before verifying I/O checks and planning for maintenance and/or commissioning projects or for use as replacements for instruments impacted by supply chain challenges
- Reduces installation risks that come with engaging multiple vendors
- Improves operational safety and mitigation risk
- Delivers best industry standards practices
- Delivers on-site instrumentation technical services, including training for maintenance personnel and support for accurate execution of preventive maintenance programs
There is no greater impact to a project’s success than having a proper plan in place and the right crew mix to implement it. Third-party field service teams perform this work safely every day and have experience in multiple control system platforms, including, but not limited to, instrumentation, calibration and field device setup. Working with plant personnel, they can effectively extend equipment lifecycle in a safe manner and help plan and prepare for future maintenance startup and commissioning needs. The right team can truly make a difference in achieving a successful maintenance project outcome.