A major food and beverage company partnered with MAVERICK to implement proven burner management optimization and an advanced process control strategy for improved process stability and energy consumption—leading to immediate 29% greenhouse gas (GHG) reduction.
OBJECTIVE
The customer engaged MAVERICK consultants to review their process and load change issues based on different moisture content of feed. The objective was to determine the best path forward regarding potential advanced process control (APC) and burner management solutions to realize improved fuel waste savings surrounding their dryer and burner systems.
RESULTS
An unstable interaction between the dryer baghouse exhaust fan and burner combustion fan was remedied and the team also implemented a rotary dryer APC program. All resulted in an immediate 29% GHG reduction—well under the customer’s initial energy usage target goal—and subsequently lowering the customer’s utility costs significantly.
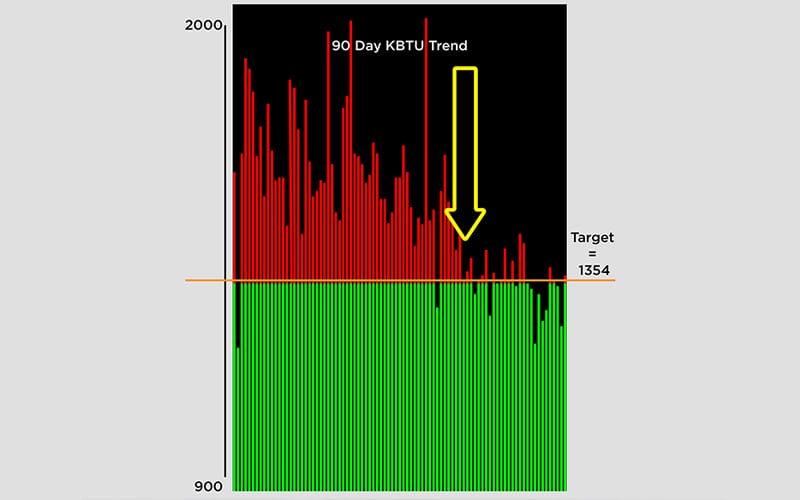
SOLUTION
- MAVERICK consultants determined the sudden load change issue was caused by the interaction between the dryer baghouse exhaust fan and the burner combustion fan. This interaction caused significant instability in the combustion fan control leading to rapid cycling and tripping of the burner, resulting in significant fuel waste.
- Once the hidden culprit was identified, the MAVERICK team guided the customer to isolate dryer baghouse exhaust fan and combustion fan control loops—providing steady-state air flow via a fixed setpoint to stabilize the burner. The team also recommended installing O2 sensors to further optimize the solution, which the customer will consider adding in a future phase.
- Along with the burner optimization, MAVERICK also helped implement feedforward control and signal damping, which compensated for varying feed rates and further stabilized process control.
- The feedforward control and signal damping were adapted via a ControlLogix APC program that was previously developed for the customer and their rotary dryer.
- The APC program was sent to the customer for installation in the existing rotary dryer process controls for product moisture control—lending additional stability and remedy for the initial load change issue.
The MAVERICK Difference
As your trusted advisor, MAVERICK has the expert knowledge and skillset to cater to the precise needs at your facility, no matter how complex the problem may be. Rely on our expert automation professionals to find the right solution for you.